
In our recent post on warehouse mistakes, we covered some of the common challenges found inside warehouses and some of the issues & challenges that many companies encounter.
This article will review a companion process by analyzing some of the common warehouse shipping mistakes evident in many organizations.
The shipping process impacts almost all organizations, directly affecting the customer and overall business effectiveness.
It can be a complex process to master, and there are plenty of opportunities to fall foul.
In this article, we’ll be looking at some of those; we’ll be looking to cover,
- What are warehouse shipping mistakes
- Common warehouse shipping mistakes
- Lost order details
- Poor selection of carriers
- Late deliveries
- Relying on a single carrier for all shipments
- Poor packaging
- Ineffective automation
- Shipments delivered to an incorrect address
- Incorrect items sent
- Incorrect shipping weight
- Poor Tracking
- Inappropriate freight class utilized
- Lack of delivery receipt
- Poor returns process
- What can businesses do to avoid warehouse shipping mistakes
What are warehouse shipping mistakes?
The shipping process involves the movement of products and the processes associated documentation.
Shipping primarily involves the movement of materials generally from one warehouse to another or from a shipping point to a customer or anything in between.
It can involve a shipping organization or a network of shipping organizations. Where the distribution network is complex, the shipping process may comprise of many stakeholders.
As you can see, within this context, the shipping process relies on a level of harmony and synchronization between participants.
It involves a series of steps that generally include
- Receipt of order
- Pick/pack goods
- Label
- Select shipping partner
- Prepare product and documents
- Shipper picks up goods
- Transport to a delivery hub
- Deliver
Mistakes usually occur when a process is deviated from or where an unexpected event occurs that had not been highlighted within risk planning (leaving the organization without an immediate solution).
Mistakes can directly impact customers, hampering business reputation.
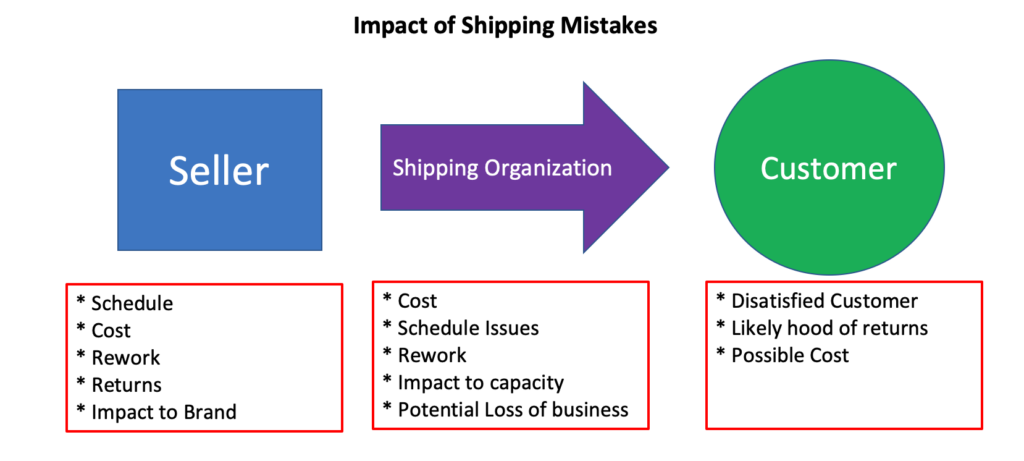
There’s also the small matter of increased costs through inefficient processes and remedying mistakes/rework.
Common warehouse shipping mistakes
Some common shipping mistakes include:

1/ Lost order details
Losing order details can often occur where the physical item(s) being delivered gets separated from the documentation or where barcodes become damaged and unreadable. Tracking data becomes ‘orphaned,’ and in the worst cases, the package is unable to be delivered.
2/ Poor selection of carriers
A shipping process is only as good as the participants who are executing it. If you’ve selected poorly performing carriers, your results are likely to be impacted. Whilst this might be primarily visible through things like late deliveries, reputational damage is also a consequence.
3/ Late deliveries
The cardinal sin of shipping. Items do not move at the schedule forecasted, and the customer doesn’t get the goods when you promised them.
While the root cause might be complex to determine given the processes at play, the customer is unlikely to be bothered by the reasons. Their goods are late, and they require the supplier to provide a simple and fast remedy.
4/ Relying on a single carrier for all shipments
How many carriers is the right number? On the one hand, relying on a single carrier can help you build a partnership with a trusted supplier partnership with a good understanding of needs and capabilities.
However, should that one carrier experience challenges such as financial problems, strikes, capacity issues, or systems failures, then you can find yourself severely hampered in the ability to move materials.
5/ Poor packaging
Improper packing amounts for a considerable quality of the shipping mistakes you’re likely to see.
The impact can be considerable; inappropriate or faulty packaging can result in damaged products.
Some examples of poor packaging include:
- Incorrect size (i.e. large package /small product)
- Inappropriate given the weight of the product
- Inappropriate given the type of product
- Inappropriate protection provided to the product where it is needed
- Packaging that is difficult to secure
Given a broad product range, you are likely to need a range of packaging. While it may seem trivial, it is better to consider the types of packaging you’ll need upfront rather than pay through delays and the cost of returns.
6/ Ineffective automation
Whilst automating processes through technology can leverage significant benefits, poor integration and synchronization between systems and partners can lead to automated processes that are severely hampered, leading to inefficiencies.
Worse than this are those organizations that fail to embrace automation at all, leaving their processes and systems a hodgepodge that does not integrate.
7/ Shipments delivered to an incorrect address
Perhaps surprisingly, given our talk of synchronized systems and complex integrated processes, shipments still get delivered to the wrong address, and it’s still one of the more frequent shipping mistakes.
There can be a multitude of root causes, the result: the delivery gets sent somewhere it shouldn’t with an unhappy customer at the end of the chain.
The business then finds itself picking up the cost and spending time in locating the item and recovering it.
8/ Incorrect items sent
This is not necessarily the fault of the shipping company but certainly the fault of the warehouse team that initiated the process.
While the fault could be down to something as simple as incorrect labeling on the stores location, the impact on the customer shouldn’t be underestimated; not only are they left with something they didn’t order, there is the returns process to consider and remedying the situation by shipping the right part. All of this adds to considerable expense and wasted time.
9/ Incorrect shipping weight
Weight remains a common mechanism for assessing shipping costs. Ineffective, badly calibrated equipment may lead to poorly estimated weights and incorrect values being used.
Further along in the process, carriers are likely to re-assess the weight of the shipment leading to excess charges if the original figure is deemed incorrect.
10/ Poor Tracking
Shipping processes rely on tracking services to correctly forecast customer deliveries and the whereabouts of stock. Ineffective or incorrect tracking can directly affect both the customer (who now wants to know where their purchase is at all stages of the Supply Chain) and the wider organization.
11/ Inappropriate freight class utilized
Using the incorrect freight class can lead to cost and/or schedule issues. Whilst lower classes might drive cheaper fees; schedules are likely to be impacted.
The inverse means that deliveries will happen more swiftly but at a higher cost. These choices need to be made with care so as not to unnecessarily impact either the customer or cost base.
12/ Lack of delivery receipt
The delivery receipt is usually signed or validated to prove product delivery. The delivery receipt can act as a device for establishing that no damage was done prior to delivery. Failing to obtain it can lead to challenges should issues be later found with the products.
Where these are captured throughout the process, the exact step where issues occurred can be identified.
Failing to capture A receipt means that should an issue occur, there will be an inability to understand where the issue occurred and where liability sits.
13/ Poor returns process
With today’s consumers ranking seamless returns processes as critical in the choice of supplier, effective returns processes are a must.
If processes are neither simple nor clear, then issues are likely to arise, leading to possible costs, disgruntled customers, and further delays.
What can businesses do to avoid warehouse shipping mistakes?
While it’s nearly always impossible to eradicate all errors, businesses can go some way to minimizing them.
Steps that can be taken include:
- Understand your process and its weaknesses – map it end to end, identify areas of concern, then look at ways of de-risking.
- Keep tabs on unexpected costs, understand their root cause then learn from them.
- Employ suitable technology to drive right first time
- Audit your data – check that it’s valid and fix it if it’s not
- Don’t cut corners – from selecting the right packaging through to obtaining correct weights and dimensions of parcels to optimize your carriers – focus on getting the job done well
- Choose the right partners – work through issues and don’t be afraid to move if you have to
- Customer is king – Focus on making your customer experience from tracking to returns to customer service simple and seamless
- Don’t forget verification processes – Verification processes help establish that steps have been made correctly; using simple verification techniques can help uncover issues before they become significant, enabling you to make corrections.
Summary
Shipping remains a key process in most businesses, one which requires careful planning in order to remain effective.
Mistakes can be commonplace; businesses require careful assessment in order to mitigate them.
In today’s complex and customer-focused business, where customer feedback can severely impact a business’s reputation, it can only take a single shipment with issues before an organization’s reputation is hit.
What are your thoughts with regards to shipping mistakes? Does your organization have common issues that we’ve not listed? Have you been part of developing mitigation strategies?
As ever, we’d love your feedback in the comments section below or via Twitter (@sanbustrain).
This article is part of our Supply Chain Guide.